冷沖拉延模計算機輔助設(shè)計
2017-01-04 by:CAE仿真在線 來源:互聯(lián)網(wǎng)
縮短模具的制作周期,提高模具的試模成功率,采用NX軟件進行先期的三維實體設(shè)計,并將模具各組成零部件進行模擬裝配,可以先期發(fā)現(xiàn)設(shè)計問題并加以解決,同時對于提升模具質(zhì)量也有積極的作用。進行冷沖拉延模具設(shè)計時,要對沖壓件材料的牌號、選用的壓力機型號、沖壓件拉延力等有個清晰的認識,明確模具結(jié)構(gòu)形式及后續(xù)模具的加工方法等事項。NX軟件中Die Design模塊提供了模具設(shè)計的常用的功能,其對冷沖拉延模具設(shè)計的一般流程如下:
1.導(dǎo)入或建構(gòu)產(chǎn)品/樣件的三維CAD模型
將沖模設(shè)計工程中構(gòu)建評估完成后的CAD模型導(dǎo)入軟件,或依據(jù)客戶的要求或設(shè)計人員的構(gòu)想,利用NX軟件系統(tǒng)下的Die Design模塊設(shè)計建構(gòu)出產(chǎn)品的三維模型。
2.對三維CAD模面進行工藝檢查
對三維CAD模面進行工藝分析包括兩個方面:產(chǎn)品工藝補充完整性和連續(xù)性;工藝補充是否存在負角。
3.創(chuàng)建拉延凸模
拉延一般有一次拉延成形和多次拉延成形,絕大多數(shù)情況下只做一次拉延成形,且做成整體式凸凹模。拉延凸模是模具的工作部分,進行拉延凸模設(shè)計要以前面做的CAD數(shù)模面為基礎(chǔ)。
4.創(chuàng)建上模本體
首先根據(jù)兩塊上模墊板之間的距離,及凸模在長、寬方向的大體尺寸,確定上模本體的外形尺寸,其次制作固定用U形槽和加強筋,最后創(chuàng)建減輕孔、鍵槽等細節(jié)。
5.創(chuàng)建拉延凹模
進行拉延凹模設(shè)計要以前面做的CAD數(shù)模型面為基礎(chǔ)。
6.創(chuàng)建壓邊圈
壓料圈對板料流動起著決定性的作用,決定著成形質(zhì)量的好壞,因此壓料圈的設(shè)計在一定意義上決定模具質(zhì)量的好壞。
7.裝配
裝配分為完全裝配和非完全裝配,此處為非完全裝配,即工藝數(shù)模、凸模、凹模、壓邊圈和壓機墊板作為單獨的部件在Assemble.prt文件下進行裝配。裝配的狀態(tài)為模具完全閉合狀態(tài)。
翼子板模具設(shè)計——雙動拉延模設(shè)計
1.導(dǎo)入?yún)⒖寄P?
啟動NX系統(tǒng),在File(菜單)下選擇File New(建立新菜單),單擊左鍵,在File New Name(新菜單命名)下輸入文件名:yi zi ban.prt,點擊Ok進入模具設(shè)計工作界面。在File下拉菜單依次選擇Import(輸入)-Part-***-gysm.prt,數(shù)模導(dǎo)入完畢(見圖1)。
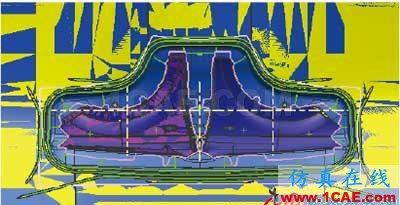
2.數(shù)模編輯
將產(chǎn)品數(shù)模、工藝補充面和工藝補充線分別分層放置。檢查產(chǎn)品數(shù)模及工藝補充面(重點檢查重面、缺面、間隙和尖角等),發(fā)現(xiàn)問題進行修補,修補完畢進行片體縫合。具體操作:分別用N-sided Surface(N邊曲面)、Trimmed Sheet(片體修剪)、Swept(掃掠)及Bridge(橋接)等命令對片體進行修補,修補后如圖2所示。在Insert(插入)下拉菜單下依次選擇Combine Bodies(組合體)—Sew(縫合),選擇片體進行縫合。
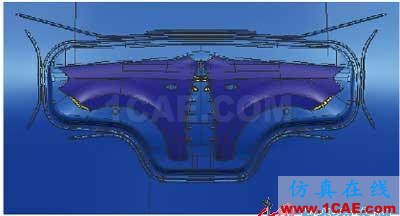
3.創(chuàng)建拉延凸模
(1)分模線拉伸實體的創(chuàng)建。分模線的編輯:用Join Curves(曲線連接)命令對分模線進行編輯。用投影命令將編輯后的分模線投影到Z平面。用Edit Curve(曲線編輯)命令對投影到Z平面上的曲線進行編輯。實體的生成:在Insert(插入)下拉菜單下依次選擇Design Feature(設(shè)計特征)—Extrude(拉伸),選擇編輯過的曲線,進行拉伸成體,如圖3所示。
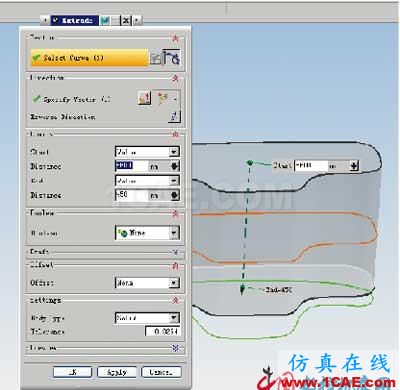
(2)實體分割。在Insert(插入)下拉菜單下依次選擇Trim(修剪)—Split Body(分割體),選擇拉伸體,用縫合的片體對實體進行分割,將分割開的實體下半部刪除,得到凸模實體(見圖4)。
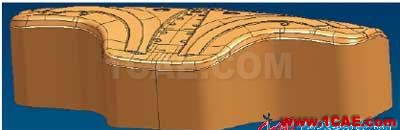
(3)凸模制作具體步驟如下:
①制作分模面退刀。在Insert(插入)下拉菜單下依次選擇Associative Copy(關(guān)聯(lián)復(fù)制)—Extract Geometry(抽取),選取分模面,點擊確定,將凸模實體隱藏,只留下分模面抽取留下的片體。在Insert(插入)下拉菜單下依次選擇Offset/Scale(偏置/縮放)—Thicken(片體加厚),選取片體確定,偏置厚度為-10mm和10mm。將偏置出的實體沿Z軸正向移動50mm,而后與凸模實體進行Subtract(減)操作,分模面退刀制作完成。
②制作導(dǎo)滑板安裝面和安全擋塊。根據(jù)制件落差確定導(dǎo)滑板長為200mm,由設(shè)計標準(導(dǎo)滑面寬度一般為分模線長度的20%~25%),設(shè)計導(dǎo)滑板安裝面為150mm×200mm,全周共設(shè)計12處;安全擋塊規(guī)格為95mm(長)×55mm(寬)×65mm(高);分別用Block(長方體)、Unite(并)和Subtract(減)等命令將導(dǎo)滑板安裝面和安全擋塊做出。
③創(chuàng)建加強筋和局部加強筋。運用Block(長方體)、Offset Face(偏置面)命令做好一條拉延筋。在Edit(編輯)下拉菜單下依次選擇Transformation(變換)—translate(平移),運用其中的Move(移動)和Copy(復(fù)制)命令,選住做好的拉延筋,按照設(shè)計標準進行移動和復(fù)制。找好CH孔和排氣孔的位置,拉延筋做避讓(見圖5)。
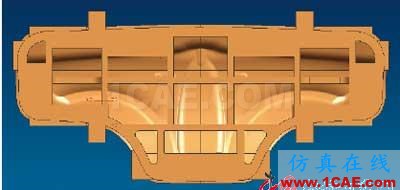
④制作固定凸模U形槽。在Tools下來菜單下依次選擇Part Families(部件族)—Browse(瀏覽)—到標準件庫選擇U形槽,根據(jù)需要進行編輯,點擊確定后進行Remove Parameters(去參),而后將U形槽復(fù)制到y(tǒng)i zi ban.prt中,再經(jīng)過Move(移動)、Unite(并)和Subtract(減)等命令將固定凸模U形槽制作出來。
⑤安裝自潤滑導(dǎo)板和翻轉(zhuǎn)吊耳。運用凸模U形槽的調(diào)用方法,依次導(dǎo)入自潤滑導(dǎo)板和翻轉(zhuǎn)吊耳,并運用Move(移動)和Copy(復(fù)制)等命令將其安裝到位。
(4)上模本體制作具體步驟如下:
①確定上模本體大體尺寸。根據(jù)兩塊上墊板之間的距離及凸模在長、寬方向的大體尺寸,確定上模本體的外形尺寸為2100mm×960mm×290mm,運用Block(長方體)命令將實體做出。
②上模本體細化制作。運用制作凸模U形槽的方法制作上下U形槽,并用此方法制作插銷式吊耳;運用凸模加強筋的設(shè)計方法制作上模加強筋;在Insert(插入)下拉菜單下依次選擇Design Feature(設(shè)計特征)—Slot(鍵槽),進行鍵槽的設(shè)計;分別用Block(長方體)、Unite(并)、Subtract(減)、Edge Blend(邊緣圓角),定位鍵槽,減輕等細節(jié)的設(shè)計;運用凸模標準件調(diào)用安裝的方法,安裝上模本體標準件,與凸模固連在一起(見圖6)。
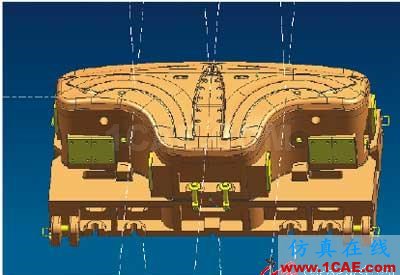
(5)凹模的制作具體步驟如下:
①調(diào)壓塊安裝臺和定位板安裝面的設(shè)計。在Insert(插入)下拉菜單下依次選擇Design Feature(設(shè)計特征)—Extrude(拉伸),選擇坯料線,進行拉伸成體;在Insert(插入)下拉菜單下依次選擇Trim(修剪)—Split Body(分割體),選擇拉伸體,用縫合的片體對實體進行分割,將分割開的實體上半部隱藏,得到凹模實體;用Offset Face(偏置面)命令將拉伸的實體向四周偏置20mm;分別用Extract Geometry(抽取)和Thicken(片體加厚)命令在實體四周生成六個小實體,選取小實體沿負Z軸移動30mm。用Cylinder(圓柱)命令生成一個直徑為60mm,高為30mm的圓柱;消參后沿坯料線外側(cè)均勻布置,同時沿坯料線布置定位板安裝面(見圖7)。
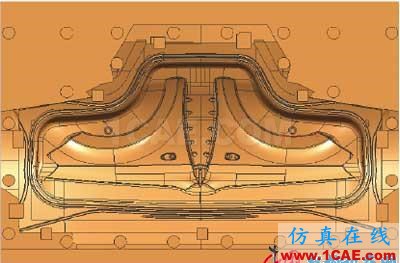
②導(dǎo)滑腿設(shè)計。根據(jù)送料高度和導(dǎo)腿強度的考慮,導(dǎo)腿設(shè)計規(guī)格為1680mm(長)×650mm(寬)×340mm(高),導(dǎo)滑板安裝面規(guī)格為150mm(長)×150mm(寬),分別用Block(長方體)、Unite(并)和Subtract(減)等命令進行制作;用Unite(并)命令將導(dǎo)滑腿和凹模連結(jié)在一塊,并用Cylinder(圓柱)和Subtract(減)等命令做出氣缸頂料過孔和CH孔,及到底標記安裝孔。
③U形槽和側(cè)筋的設(shè)計。運用制作凸模U形槽的方法制作U形槽,并用此方法制作插銷式吊耳,用Block(長方體)、Chamfer(倒角)等命令制作側(cè)筋。
④細節(jié)設(shè)計。分別用Block(長方體)、Unite(并)、Subtract(減)和Edge Blend(邊緣圓角)等命令進行滾輪定位臺、正向標示及減輕等細節(jié)的設(shè)計。運用凸模標準件調(diào)用安裝的方法,安裝凹模標準件。
(6)壓邊圈的制作具體步驟如下:
①凸模讓位孔、內(nèi)導(dǎo)滑面及上墩死臺等部分的制作。運用Extrude(拉伸)命令,選擇制作凸模時編輯過的分模線,進行拉伸成體,再用Offset Face(偏置面)命令將拉伸的實體向四周偏置3mm,成體后將凹模制作時隱藏的實體調(diào)出,用Subtract(減)命令將兩實體做差;用Cylinder(圓柱)、Block(長方體)、Unite(并)、Subtract(減)等命令制作導(dǎo)滑板安裝面、墩死圓臺和定位板讓位孔等。
②導(dǎo)滑腿設(shè)計。此部分設(shè)計應(yīng)與凹模導(dǎo)滑腿設(shè)計相結(jié)合,依據(jù)送料高度和導(dǎo)腿強度的考慮,導(dǎo)腿設(shè)計規(guī)格為1680mm(長)×650mm(寬)×590mm(高),導(dǎo)滑面規(guī)格為150mm(長)×150mm(寬)。分別用Block(長方體)、Unite(并)、Subtract(減)等命令進行制作。
③U形槽和側(cè)筋的設(shè)計。運用制作凸模U形槽的方法制作U形槽,并用此方法制作插銷式吊耳,用Block(長方體)、Chamfer(倒角)等命令制作側(cè)筋,制作完畢后用Unite(并)命令將導(dǎo)滑腿、U形槽、側(cè)筋和壓邊圈本體連結(jié)在一起。
④細節(jié)設(shè)計。分別用Block(長方體)、Unite(并)、Subtract(減)、Hole(孔)和Edge Blend(邊緣圓角)等命令進行基準孔、正向標示、減輕、避讓和窺視孔等細節(jié)的設(shè)計;運用凸模標準件調(diào)用安裝的方法,安裝壓邊圈標準件。
(7)裝配具體步驟如下:
①分別建立shangmo.prt、aomo.prt及yabianquan.prt文件,將凸模和上模本體連同標準件導(dǎo)入shangmo.prt文件,將凹模實體連同標準件導(dǎo)入aomo.prt文件,將壓邊圈實體連同標準件導(dǎo)入yabianquan.prt文件。建立新文件夾,命名為:yi zi ban,將shangmo.prt、aomo.prt、yabianquan.prt和gysm.prt連同壓機墊板放入“yi zi ban”文件夾中。
②新建assemble.prt文件,在Assemblies下拉菜單下依次選擇Components(組件)—Add Components(添加組件),將shangmo.prt、shangmo.prt、aomo.prt、yabianquan.prt、gysm.prt以及yajidianban.prt文件依次導(dǎo)入,完成裝配。
結(jié)語
根據(jù)冷沖模具設(shè)計的基礎(chǔ)知識和設(shè)計規(guī)則,利用NX進行冷沖拉延模具實例設(shè)計,驗證了直接根據(jù)三維造型產(chǎn)品的三維數(shù)據(jù)來完成整個模具結(jié)構(gòu)的設(shè)計工作,能大大縮短模具設(shè)計周期,提高工作效率。
相關(guān)標簽搜索:冷沖拉延模計算機輔助設(shè)計 Dynaform鈑金分析培訓(xùn) Dynaform汽車模具仿真分析培訓(xùn) Dynaform技術(shù)教程 Dynaform資料下載 Dynaform分析理論 Dynaform軟件下載 Fluent、CFX流體分析 HFSS電磁分析 Ansys培訓(xùn) Abaqus培訓(xùn) Autoform培訓(xùn) 有限元培訓(xùn)